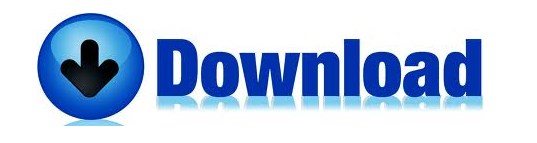
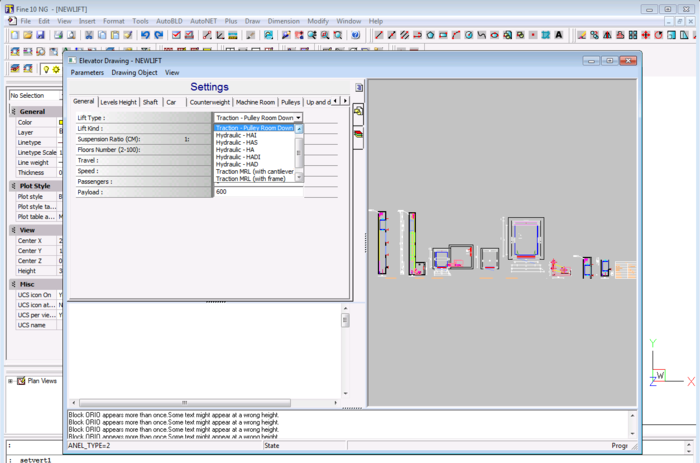
Furthermore, when long connection cables are used between motor and power converter, high dv/dt voltages, which are characteristic in PWM signals, might cause over voltages at motor terminals which could damage seriously the winding insulation.Ī possible solution to identify these problems is to add a new step into the design process previously to the prototyping stage, where the behavior of the machine into the final application is analyzed, evaluating the interaction between different elements of the system. For instance, the large amount of harmonic components contained in a PWM wave can increase the iron losses.
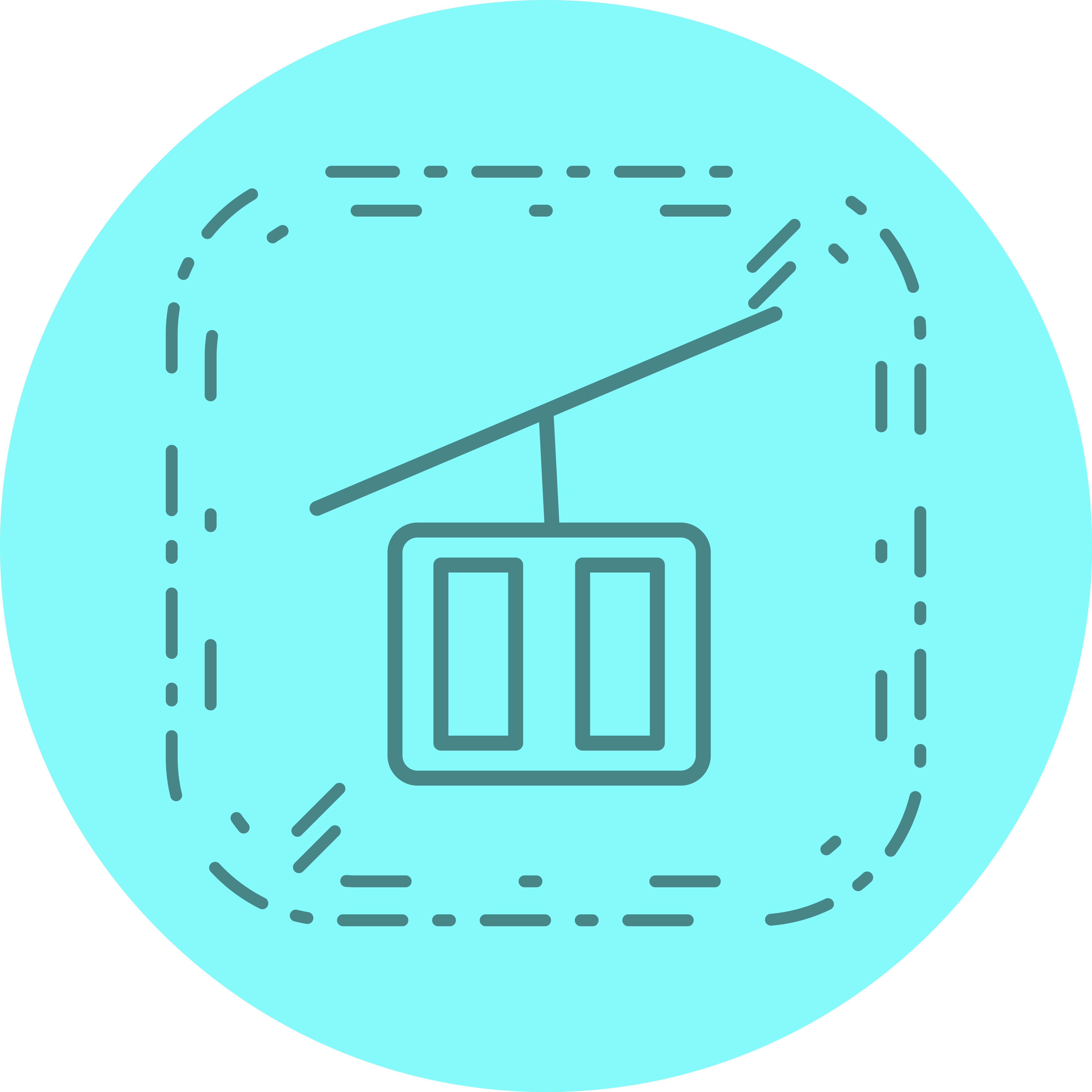
At the same time, machine performance could be negatively affected by the Power Converter. For example, at low speeds, the torque ripple produced by the machine could cause undesirable speed pulsations and inaccuracies in motion control. Actually the electromagnetic properties of the machine can influence the overall performances of the system, or the performances of the motor can get worse due to the influence of other components that are connected to the motor. Classical electric machine design processes normally do not take into account some specific aspects (PWM voltage supply, mechanical resonances, etc) of the application where the motor is integrated.
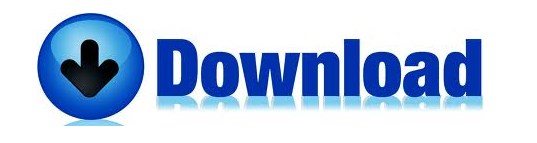